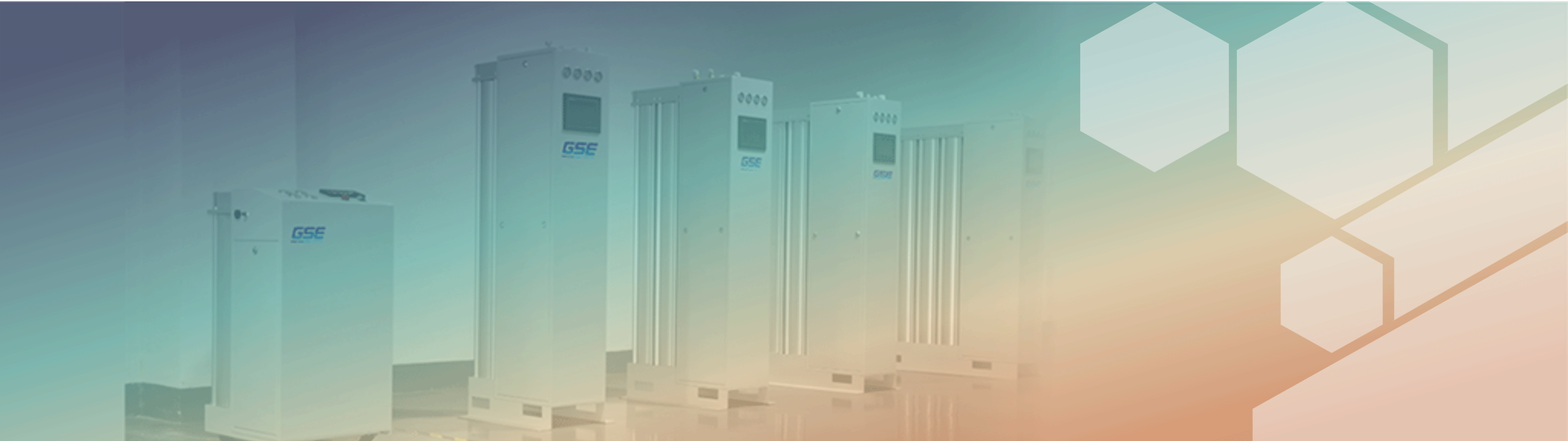
NPM-20P Nitrogen Generator (N₂-Generator) – Efficiency and Quality for Modern Electronics Manufacturing
N₂-Generator is an indispensable component in SMT manufacturing processes. By providing a continuous supply of pure nitrogen gas on-site, an N₂-Generator enhances production quality, reduces operating costs, and optimizes the entire manufacturing chain.
Nitrogen is used to create an inert atmosphere that prevents oxidation, improves the quality of solder joints, and ensures a stable production environment. Compared to the traditional use of nitrogen in bottles or tanks, a nitrogen generator offers numerous advantages.
With NPM nitrogen generator, you are investing in an efficient, reliable, and sustainable solution to meet the demands of modern electronics manufacturing.
Smartlink-SMT is happy to assist you in selecting the optimal size and model tailored to your specific consumption needs.
Nitrogen – an indispensable element in industry
Nitrogen is a colorless and odorless gas with a density of 1.251 g/L, which is lower than that of air. It constitutes 78.08% of the Earth’s atmosphere and is one of the primary components of air. Thanks to its chemical inertness, nitrogen reacts minimally with other substances at room temperature. This property makes it an ideal inert shielding gas, protecting sensitive processes and materials from unwanted chemical reactions.
PSA Nitrogen Generator: how does it work?
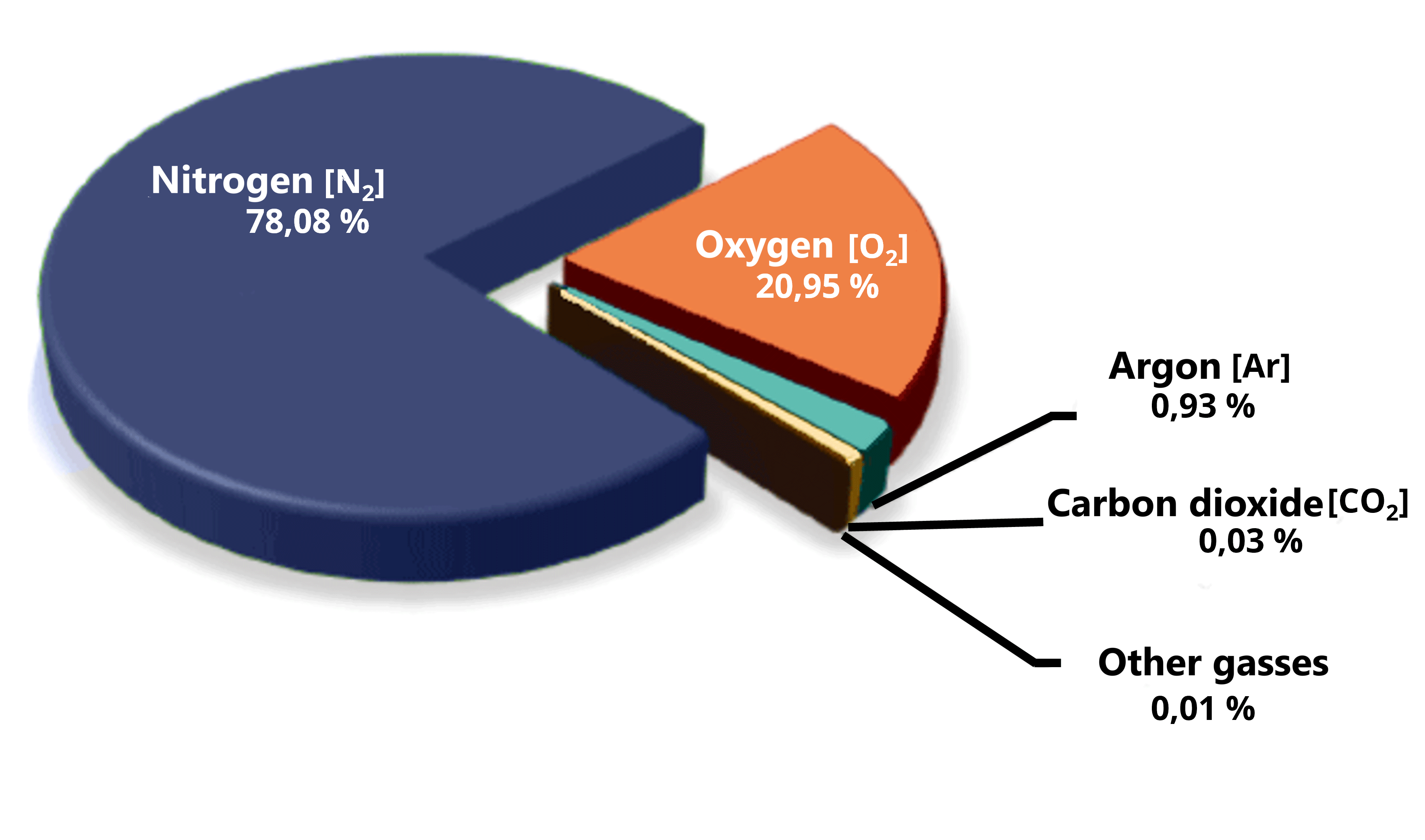
PSA nitrogen generator (Pressure Swing Adsorption) separates oxygen and nitrogen from ambient air through a physical process to produce high-purity nitrogen. The process relies on the differing adsorption capacities of oxygen and nitrogen on carbon molecular sieves.
Operating Process of a PSA Nitrogen Generator
PSA nitrogen generators typically utilize two parallel adsorption towers. While one tower adsorbs oxygen, the other regenerates. This alternating operation ensures a continuous supply of high-purity nitrogen.
Thanks to this technology, PSA nitrogen generators are a practical and widely used solution for gas separation processes, especially in industries requiring high-purity nitrogen.
Technical Advantages of Nitrogen Generators:
Why an N₂-Generator is your best solution:
Applications in SMT Production
Specifications
Contact us directly for a free consultation.
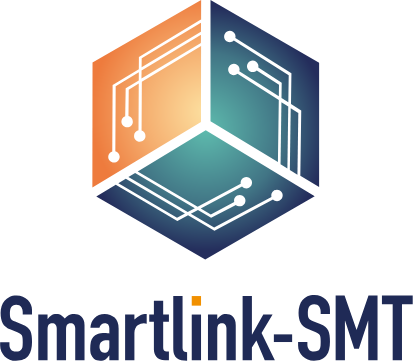
Navigation
© Copyright 2025 | SmartLink